pallet
assembly system for plastic parts
TQC have performed a number of sophisticated
pallet based automatic assembly and test projects for several demanding applications. The
system shown here was designed and engineered for the automation of a glove box latch
assembly for a high volume automotive manufacturer. The latch can be produced in different
formats for different applications, hence a modular automation approach has been adopted.
The production volumes are large and hence the machine cycle time is relatively short. The
system was supplied to Southco Manufacturing winners of the Management Today 2001 Best
Factory Award.
TQC have provided multi station industrial automation
production lines and robot workstations in different applications, ranging from automotive
parts manufacture, transfer of green state ceramic components, medical device assembly and
precision automation at high speeds.
This particular assembly cell is engineered to have
minimum operator involvement. All parts are automatically fed from vibratory bowl feeder
systems where box quantities of product are loosely tipped into the feeding bowls.
The output from the cell is automatically placed
into shipping cartons at the unload station.
The system takes six parts, including plastic mouldings
and springs to assemble the latch. The part is tested for correct operation within the
cell after the assembly operation is complete. The good parts are automatically ink jet
marked.
The facility is completely guarded with aluminium extruded
frames and clear guard panels. All of the openings for the bowl feeders are outside the
guarded area, allowing the operator to top up the bowls without stopping the machine. The
deposit point for the assembled and tested product is also outside of the guarded area.
The carton filling system also has an automatic carton change facility.
The production line has been engineered
to allow for future variants of the similar high volume automotive latch mechanisms to be
assembled on the same production line. The design of the assembly cell follows a modular
approach; each element is wired and piped back to distribution points on each station.
The system incorporated a PLC control system complete with
Human Machine Interface Panel. The HMI unit consisted of a display and function buttons,
this was used to provide status information on the machine for diagnostic purposes and
manual setting operations at each station.
Attention was paid to minimising noise levels on the shop
floor by using acoustic covers. In addition, there was a roof on the guarding system over
the pallet conveyor area for additional noise reduction and to keep the whole system
clean.
Similar systems have been engineered by TQC to assemble a diesel
fuel switch, a distributor and domestic appliance switches.
TQC used its professional engineering project
management approach to ensure that this project met both timescale and budget
requirements.
TQC welcomes the opportunity to design
and manufacture complete automation systems to client specifications.
Contact our Engineers to advise you on your automation project.
TQC Ltd, Hooton Street,
Carlton Road,
Nottingham, NG3 2NJ, United Kingdom
Tel: +44 (0)115 9503561
Fax: +44 (0)115 9484642
E-mail: sales@tqc.co.uk
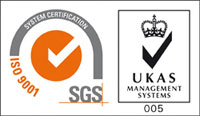
|
|